Terex Explorer 5500 Truck-Mounted 130 Tonne Crane
This is my most complex and challenging project to date. The Terex Explorer 5500 truck-mounted crane.
The Terex 5500 is a heavy-lift truck-mounted crane capable of lifting 130 tonnes with a boom height of 60 metres and the maximum jib length of 30 metres. It's powered by a Scania DC13 500 engine and has all-wheel steering on a 10x5 chassis layout. The overall dimensions in transport mode is 14.3 metres long, 2.85 metres wide and 3.99 metres high, making the 1:24 scale model around 585mm (L) x 119mm (W) x 166mm (H).
The project, as with the last two models (Lockheed Martin AN-TPQ53 Radar System and Kamaz Red Bull Rally Truck) started out with purchasing a high quality 3D virtual model from TurboSquid.com. The first process is to import the virtual model into KeyShot, which usually opens 'full-size', in other words, the size of the actual subject. Having located a technical document from Terex, I check just one dimension against the 'virtual' model. I then reduce the overall size to 1:24 scale by entering a factor of 0.041667.
With this relatively new (to me) method of model-making, the term 'multi-media' refers to the different types of materials and processes, as opposed to using proprietary kits and kit-bashing. Basically, the three main methods of modelling in this way are resin 3D printing, CNC machining and traditional scratch-building and very few proprietary kit parts are used, apart from the odd detailing items.
Most 'virtual' 3D models include a structured file system consisting of multiple parts allowing selection of individual items. Once a part is selected, it can be displayed on its own, ready to export as an STL file which is required by the 3D resin printer. All three 'virtual' 3D models that I have used in the last three projects have been outstanding quality but very often, many of the 'virtual parts', although display correctly on screen can be non-manifold.
This means that when directly exported to the printer, any non-manifold files will not slice and therefore fail to print. Therefore, any non-manifold parts can either be imported into other software such as Microsoft's 3D Builder to try and resolve any non-manifold errors, or simply re-drawn in 3D CAD. Many of the parts in this scale model were re-drawn due to non-manifold geometry.
Chassis...
I started by making the chassis from three pieces of CNC machined 3.2mm plasticard, which, at 430mm long just fitted on the machine. I was glad it did fit, so that it didn't require joining sections together which would reduce the strength of this large and rather heavy model. As a rule, I tend not to model anything that won't be seen, although I did print and install all five axles, four of which include the differentials detailing...and they can't be seen on the finished model! The wheel (rim) and tyre, unfortunately was combined as a single part in the virtual model and I had trouble separating the geometry, so I had to print them as combined.
However, this wasn't an issue, as painting the rims and tyres later on proved relatively easy. Once the basic chassis and upper superstructure was completed, I could prime and paint to make things easier as the rest model is added.
Crane Boom...
Whilst the Mono X 3D printer has a large build volume, obviously it was not large enough to print the main boom sections and lattice fly-jib. Luckily, the fly-jib wasn't non-manifold and was created as a single part in the virtual 3D model. The main boom section was re-drawn in two sections to fit on the printer's build plate. Once printed, these two sections were joined, and I added some internal stiffeners to ensure a good bond, considering the overall length. However, the lattice fly-jib had to be printed in three sections and I used 3D Builder software to 'slice' the STL file into three sections. Unfortunately, the print quality isn't the best it could be, due to the amount of supports required during the printing process. Even with copious amounts of filling and sanding of the intricate lattice work, the finish could have been better.
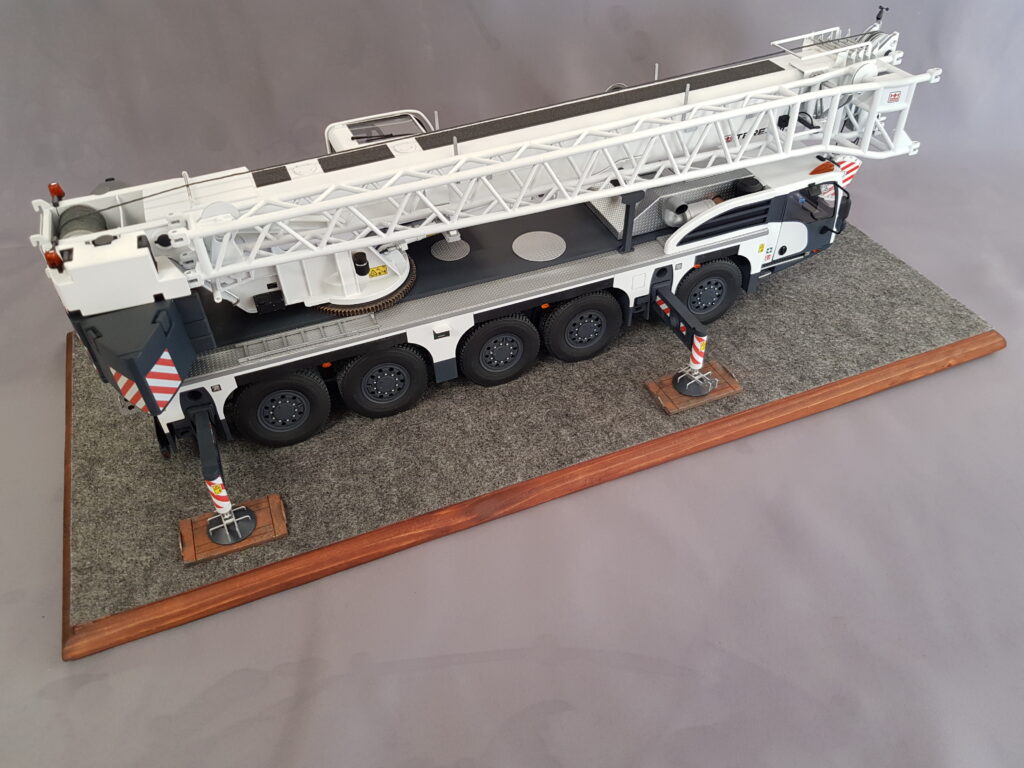
More to follow soon...